FIELD OF THE INVENTION
- The Maximum Number Of Ignition Retries
- Maximum Amount Of Ignition Attempts System Is Locked On My Rheem Water Heater
- Maximum Amount Of Ignition Attempts Rheem
- Maximum Amount Of Ignition Attempts
- Intelli Vent Maximum Amount Of Ignition Attempts
This invention relates to an ignition timing control apparatus for an engine, and particularly to an ignition timing control apparatus for an engine capable of enhancing its drivability by changing an EGR rate in a non-stage manner and adjusting the ignition timing in accordance with the EGR rate.
Other causes of the ignition/flame failure: Low pressure – the manifold gas pressure cannot be adjusted so if it is off by 0.3' W.C. You must replace the gas control valve. Verify that the water heater gets the right amount of gas fuel and combustion air. Low voltage – the voltage must be between 115 and 125 VAC. I have Rheen Model 42VP75FW - and its not working - the lights on it tells me maximum amount of ignition attempts has been reached and system is in lockout - this makes sense as when I reset it it tries to get going several times and then this light goes on and its silent. DO NOT approach the engine between failed start attempts as the starter will attempt to start again if the engine is still enabled. ICESTARTPCT overrides the throttle setting during start. ICESTARTTIME controls the maximum amount of time the starter will run in each start attempt. ICESTARTDELAY sets a delay between start attempts. My Richmond Water Heater (Model 6G40PVW-40F) works for 7 minutes then it shuts down and locks out showing the 'Maximum amount of ignition attempts has been reached and system is in lockout' code. The ignitor stick glows red and the burner fires up and burns for 7 minutes then it shuts down and tries to start back up, the ignitor stick glows red.
BACKGROUND OF THE INVENTION
An engine usually includes an exhaust gas recirculation (EGR) mechanism for reducing the harmful components contained in the exhaust gas by recirculating the exhaust gas into the gas intake system.
That is, as is shown in FIG. 6, in an engine 202, an intake pipe 206 forming an intake passage 204 and an exhaust pipe 210 forming an exhaust passage 208 are disposed in a connected relation. An EGR valve 212 is attached to the intake pipe 206. Disposed between the EGR valve 212 and the exhaust pipe 210 is an EGR pipe 216 forming an EGR passage 214.
In an intermediate portion of the EGR pipe 216, an EGR switch-over valve (VSV) 218 is disposed. This EGR switch-over valve 218 is operation-controlled by a control means (ECU) 220.
Input into the control means 220 are data of the driving state of the engine 202 such as cooling water temperature, intake pipe absolute pressure PM, intake-air temperature, throttle opening degree, number of engine revolution (engine rotational speed), etc.
The control means 220 is connected to a crank angle sensor 222 mounted on the engine 202 and adapted to detect the crank angle, and is also connected with an ignition mechanism (ignitor) 224 for the engine 202. This ignition mechanism 224 is of an electronic spark advance (ESA) type.
In FIG. 6, the controlling of the EGR rate to the intake system is performed by an on/off operation of the EGR valve 212. This being the case, the ignition timing at this time is either held constant whether the recirculation of exhaust gas is effected or not, or adjusted in two stages depending on whether the recirculation of exhaust gas is effected or not.
On the other hand, in an ignition timing control operation of an ignition mechanism of a distributor type instead of the ignition mechanism of an electronic spark advance type, the ignition timing is held constant whether the recirculation of exhaust gas is effected or not.
One such ignition timing control apparatus is disclosed, for example, in Japanese Patent Early Laid-open Publication No. Sho 57-179370 and Japanese Utility Model Early Laid-open Publication No. Sho 61-66667. One, which is described in Japanese Patent Early Laid-open Publication No. Sho 57-179370, is designed such that if, at the time a non-operating state of the EGR valve is detected, the engine speed and the value of a signal representing the amount of air intaken are within the ranges of the amount of intaken air and the engine speed on level ground, then the ignition timing is optimally corrected in order to prevent the occurrence of knocking of the engine also on a high land.
Another apparatus, which is described in Japanese Utility Model Early Laid-open Publication No. Sho 61-66667, is designed such that the ignition timing is corrected in accordance with EGR based on the change in the rate of EGR.
There is conventionally an inconvenience in that, since the control means does not have a single kind of ignition timing map, the ignition timing at the time that recirculation of exhaust gas is not effected is excessively spark advanced, thus exerting adverse affects on drivability, emission, etc.
Also, because of the above-mentioned reason, the exhaust gas recirculation mechanism cannot be turned on/off positively depending on driving conditions of the engine and, therefore, improvement was demanded.
Further, even in case the control means is provided with two kinds of ignition timing maps for performing an on/off operation for the exhaust gas recirculation mechanism, there is an inconvenience in that an attempt is made to control the rate of EGR, and the ignition timing is excessively spark advanced or excessively spark halted because the required ignition timing is uselessly changed due to difference in the rate of EGR.
Therefore, an object of the present invention is to provide an ignition timing control apparatus for an engine, in which a duty-controlled EGR rate regulating solenoid valve is disposed midway along an EGR passage intercommunicating an exhaust passage and an intake passage, and by adjusting the ignition timing in accordance with a duty rate which controls the EGR rate regulating solenoid valve, the EGR rate is changed in a non-stage manner and the ignition timing is optimally adjusted in accordance with this EGR rate, thereby enhancing the drivability and obtaining the most appropriate exhaust emission.
In an attempt to achieve the above object, in an engine including an exhaust gas recirculation mechanism for recirculating a part of the exhaust air into the gas intake system, the present invention is characterized in
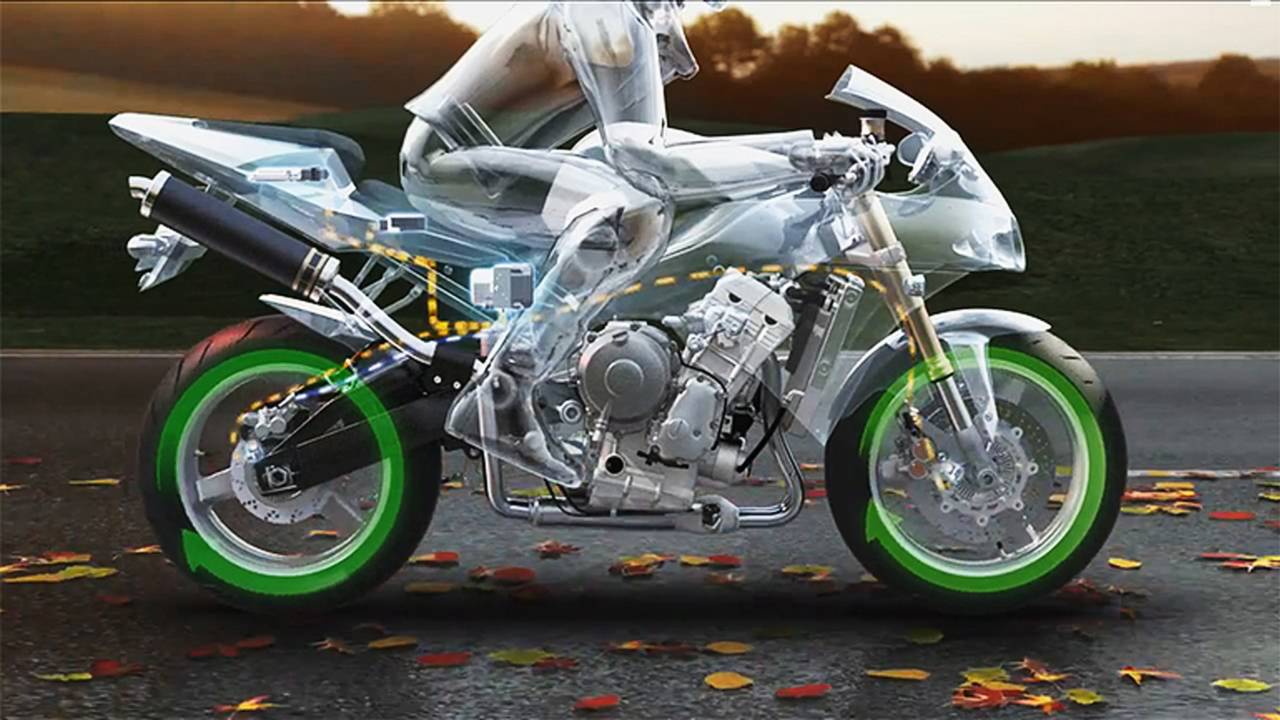
a duty-controlled EGR rate regulating solenoid valve is disposed midway along an EGR passage intercommunicating the exhaust passage and the intake passage, and means for controlling the activation of the engine ignition mechanism is provided in order to adjust the ignition timing in accordance with a duty rate which is applied to said EGR rate regulating solenoid valve.
According to the constitution of the present invention, since the control means actuates the ignition mechanism in accordance with the duty rate applied to the EGR rate regulating solenoid valve to adjust the ignition timing, the ignition timing can be optimally set when the EGR rate is changed in a non-stage manner and by this, the EGR rate can be positively controlled to enhance the drivability and to obtain the most appropriate exhaust emission.
BRIEF DESCRIPTION OF THE DRAWINGS
One embodiment of the present invention will be described in detail with reference to the drawings, in which:
FIG. 1 is a block diagram of an ignition timing control system apparatus for an engine;
FIG. 2 is a flowchart for explaining the operation of the FIG. 1 system;
FIG. 3 is an explanatory view of an ignition timing map where the EGR duty rate is between 0% and 100%;
FIG. 4 is an explanatory view of an ignition timing map where the EGR duty rate is 0%;
FIG. 5 is an explanatory view of an ignition timing map where the EGR duty rate is 100%; and
FIG. 6 is a block diagram of a conventional ignition timing control system apparatus.
DETAILED DESCRIPTION
FIGS. 1 through 5 show one embodiment of the present invention. In FIG. 1, the numeral 2 denotes an engine, 4 an intake pipe, 6 an intake passage, 8 an exhaust pipe, and 10 an exhaust passage. The intake pipe 4 and the exhaust pipe 8 are interconnected by an EGR pipe 14 forming an exhaust gas recirculation mechanism 12.
This EGR pipe 14 forms an EGR passage 16 for intercommunicating the intake passage 6 and the exhaust passage 10. That is, an EGR inlet port 18 as the start of the EGR passage 16 opens into the exhaust passage 10 and an EGR circulation portion 20 as a terminal of the EGR passage 16 opens into the intake passage 6. Midway along this EGR passage 16, a duty-controlled EGR rate regulating solenoid valve 22 is disposed in order to regulate the rate of EGR by opening and closing the EGR passage 16. This EGR rate regulating solenoid valve 22 is duty-controlled by a control means (ECU) 24. That is, the valve 22 is activated by ECU 24 between a state of 0% of EGR duty (totally closed state) and a state of 100% of EGR duty (totally opened state). By this, the EGR rate effected by the EGR passage 16 can be controlled in a non-stage manner as defined by the continuum of duty rates between 0% and 100%.
Input into this control means 24 are data representing cooling water temperature, intake pipe absolute pressure PM, intake air temperature, throttle opening degree, the number of engine revolution (i.e. engine rotational speed) NE, and a crank angle of the engine from a crank angle sensor 26 attached to the engine 2.
Further, this control means 24 is operated to control the activation of an ignition mechanism 28 of the engine 2 in order to adjust the ignition timing in accordance with the duty rate applied to the EGR rate regulating solenoid valve 22. The control means 24 has an ignition timing map (see FIG. 4) for use at the time the EGR duty is 0% (EGR is in the totally closed state) and an ignition timing map (see FIG. 5) for use at the time the EGR duty is 100% (EGR is in the totally open state). Those ignition timing maps shown in FIGS. 4 and 5 are decided by, for example, the engine rotational speed NE and the intake pipe absolute pressure PM. Accordingly, when the EGR duty is 100%, the FIG. 5 map indicates that the ignition timing is to be spark advanced. For example, the ignition timing is 20 BTDC when the EGR duty is 0% and the ignition timing is 40 BTDC when the EGR duty is 100%, at a certain lattice point defined by the values of NE and PM (see FIGS. 4 and 5) That is, for given values of NE and PM, FIGS. 4 and 5 yield 20° BTDC and 40 ° BTDC, respectively, as functions of NE and PM. Thus, for example, 20° BTDC=f(NE, PM).
And in case a vehicle runs at this lattice point, the ignition timing control at the time the EGR duty is changed between 0% and 100% is decided with reference to the ignition timing map of FIG. 3. That is, for given values of NE and PM, when the EGR duty is something other than 0% and 100%, interpolation is effected with reference to FIG. 3. Accordingly, in case the EGR rate is changed in a non-stage manner, the best ignition timing can be obtained based on the ignition timing decided by the ignition timing maps of FIGS. 3, 4 and 5.
It will be evident from the foregoing and following discussions that ECU 24 can be implemented using a conventional microprocessor circuit.
Next, operation of this embodiment will be described with reference to the flowchart of FIG. 2.
In the control means 24, when a program is started (step 102), first, the data representing the engine rotational speed NE, intake pipe absolute pressure PM, throttle opening degree, cooling water temperature, etc. are input (step 104), and then a duty rate for the EGR rate regulating solenoid valve 22 is calculated from this data (step 106).
Next, the control means 24 is operated to control the activation of the EGR rate regulating solenoid valve 22 in accordance with the calculated duty rate (step 108).
Further, the control means 24 is operated at 110 to control the activation of the ignition mechanism 28 and thereby implement the ignition timing decided based on the ignition timing maps of FIGS. 3 through 5 with reference to the EGR duty rate calculated at 106. That is, the control means 24 is operated to actuate the ignition mechanism 28 at the ignition timing decided by the ignition timing map shown in FIG. 4 when the EGR duty is 0%, the control means 24 is operated to actuate the ignition mechanism 28 at the ignition timing decided based on the ignition timing map shown in FIG. 5 when the EGR duty is 100%, and the control means 24 is operated to actuate the ignition timing mechanism 28 at the ignition timing decided based on the ignition timing map of FIG. 3 when the EGR duty is something other than 0% and 100% (step 110).
As a result, since the EGR rate regulating solenoid valve 22 is duty-controlled by the control means 24, the EGR rate can be changed in a non-stage manner and since the ignition timing is optimally adjusted in accordance with the duty rate applied to the EGR rate regulating solenoid valve 22, the drivability can be enhanced and there can be obtained the most appropriate exhaust emission. Further, since the ignition timing is changed in accordance with the EGR rate, the drivability can be enhanced by positively changing the EGR rate (or turning off the EGR).
Furthermore, since the ignition timing maps of FIGS. 4 and 5 are only, for example, two-dimensional maps of engine rotational speed (NE) X intake pipe absolute pressure (PM), and do not require a three-dimensional map of engine speed NE X intake pipe absolute pressure PM X EGR duty rate, the control means 24 can be simplified and the capacity of the control means 24 can be reduced.
As apparent from the foregoing detailed description, according to the present invention, since a duty-controlled EGR rate regulating solenoid valve is disposed midway along an EGR passage intercommunicating an exhaust passage and an intake passage, and means for controlling the activation of the engine ignition mechanism is provided in order to adjust the ignition timing in accordance with a duty rate applied to the EGR rate regulating solenoid valve, the EGR rate can be changed in a non-stage manner and the ignition timing can be optimally adjusted in accordance with the duty rate applied to the EGR rate regulating solenoid valve, thus enhancing drivability by positively controlling the EGR rate and obtaining the most appropriate exhaust emission.
Although a particular preferred embodiment of the invention has been disclosed in detail for illustrative purposes, it will be recognized that variations or modifications of the disclosed apparatus, including the rearrangement of parts, lie within the scope of the present invention.
Ignition Systems
Basics to High Performance
The job of an ignition system is to generate the spark energy needed to ignite the air/fuel mixture in an engine's cylinder. The main components of this system consist of an ignition coil, coil driver, distributor, spark plug wires, and spark plugs. This page will concentrate on the generation of the high voltage needed to produce a spark, and will begin with a basic ignition style and progress to performance types.
Magnetos
The most basic form of an ignition system is the magneto. Although it was one of the first styles built, it remains in use today. Using the example of a small engine such as a lawn mower or chainsaw, a basic magneto begins with a hub containing magnets which is attached to the crankshaft. As the crankshaft turns these magnets spin past a primary coil of wire to produce a current similar to a generator. The faster the engine runs the more power is generated by the magneto. A set of contacts (points), with a condenser to reduce contact arc wear, switches the current on and off in this primary coil. This process induces a pulse of a few hundred volts into a secondary coil each time the contacts open. The secondary coil has a much higher number of wire turns (typical ratio of 100:1) which acts to multiply the voltage into tens of thousands of volts to produce a spark. The points are activated by a lobe on the crankshaft to produce the spark at the right time (ignition timing). Newer type magnetos use electronic controls instead of points and can offer better timing control. Since magnetos generate their own electricity they are suitable for products that do not have room to carry and recharge batteries, such as lawn mowers, chainsaws, outboard motors and some small displacement motorcycles, etc. Some aircraft still use magnetos (although more complex) as do some racecars. It should be noted that magnetos are not free energy devices. They do place load on a engine like a generator would, with some very large ones actually drawing a moderate number of horsepower.
Kettering Ignition
This battery powered ignition system was first developed by Charles Kettering. A battery replaced the generator portion of a magneto with a battery. A set of contacts (points) and a condenser, switched current from the battery into an ignition coil primary winding. When the points were opened the current would stop and the magnetic field that built up in the primary would collapse, inducing a few hundred volts into the secondary winding of the ignition coil. Again as with a magneto, a turns ratio of 100:1 would yield a secondary voltage that would be in the ten's of thousands of volts. One main advantage of this type of ignition over a magneto is that it can produce strong sparks at low rpm as it doesn't rely on a generator as a primary power source. A condenser is still used to limit the arc current across the points reducing wear. The condenser also helps discharge the coil faster allowing the magnetic field to more fully transfer into the secondary. As engines were built with more cylinders, a device called a distributor was added to the ignition system. A distributor does as the name implies, it distributes the spark to the correct cylinder. A distributor is basically a housing with a shaft that is driven by the engine. Lobes on the shaft activate the points, and a rotor on top of the shaft directs the spark to contacts located in a distributor cap placed on top. From this cap, spark plug wires connect to each individual spark plug.
As expressed earlier, the output of an ignition coil is the result of the primary induced voltage multiplied by the turns ratio. The higher the primary induced voltage (which should not be confused with the battery supply voltage), the higher the coil's output voltage for a given turns ratio will be. The primary induced voltage is a function of the strength of the magnetic field produced by battery current, and charge time (dwell) controlled by the closed time of the points. If a condenser was not present, the primary current would mostly bleed off through the arc produced when the points open, resulting in a very weak spark being produced from the secondary. We will expand on this later as it pertains to performance ignition systems. Aside from the high voltage produced from a coil, the output current is also important as it directly relates to spark duration which does the actual work igniting a fuel mixture.
Electronic Ignition
The initial design of the electronic ignition employed a high voltage transistor to switch current into the ignition coil instead of points. In early designs, a set of points were used to trigger the transistor and since the current required was very low, there would be no contact wear through arcing which allowed longer life of the points. The condenser could be eliminated as the points had no further arcing issues. Utilizing a transistor enables faster switching of the coil primary. This allows higher current transfer to take place resulting in more coil output. Further improvements included the use of a magnetic reluctor pickup to replace mechanical points. This type of pickup uses a small toothed collar to replace the lobes on the distributor shaft. As the teeth pass a bobbin of wire and magnet combination, a small signal is produced to trigger the transistor circuit. Another variation uses Hall Effect technology where the bobbin of wire is replaced by a special transistor. Some distributors were also designed with an optical pickup in which an infrared light beam was interrupted by a notched wheel on the distributor shaft. Some modern ignitions use separate coils for each spark plug which are triggered from sensors directly on the crankshaft and camshaft through an onboard computer.
Inductive Discharge vs Capacitive Discharge Ignition (CD)
All of the above descriptions are examples of Inductive Discharge type ignition systems. The first high performance ignition system design was the Capacitive Discharge Ignition which uses high voltage stored in a capacitor to induce the few hundred volt pulse into the secondary instead of generating it in the primary as with an inductive system. In a CD system a high voltage oscillator circuit charges a capacitor. When it is time for a spark, another circuit discharges the capacitor into the coil primary. The voltage produced from the secondary is in the same proportion as with an inductive system. For example if the capacitor is charged to 400 volts, a 100:1 coil will produce 40,000 volts (or there abouts). CD ignitions have certain limitations depending on design. As an example if the oscillator is not powerful enough, the capacitor will not recharge quick enough and the ignition will have an RPM limitation. As you engineer more powerful oscillators, power consumption also increases. As the size of the capacitor is increased, the output of the ignition also increases, however the oscillator must be made more powerful. Certain tradeoffs must be made in design for a particular application.
Compared to inductive systems of the day, CD systems were more powerful since higher primary voltages could be discharged into the coils. One inherent limitation to a CD system is that the spark duration is short due to small capacitors used. As mentioned earlier, spark duration does the actual work burning an air fuel mixture, the voltage is used to initialize current flow across a spark plug gap. Due to the high primary currents of an inductive system, spark duration is naturally longer. Some Manufacturers of CD ignition systems provide multiple sparks to increase overall spark duration. Of course, as mentioned before, capacitors take time to charge up so there are limitations as to what RPM levels a CD system can maintain multiple sparks.
Today with improvements in technology, inductive ignition systems can be made more powerful with special transistors (Mosfets) switching the coil. These devices have higher breakdown/clamping voltages which allow the primary voltage to increase ( 550+ volts) resulting in higher secondary voltages. This coupled with the inherent long duration makes for a powerful ignition which has the capability of also going multi spark. Inductive ignition systems are emerging as the new high power ignition systems.
More Voltage ?
There is some argument that output voltage of an ignition system does not have to exceed 35,000 to 40,000 volts as normal demand doesn't exceed this. The voltage required to initiate a spark across a spark plug gap depends on a number of conditions including, but not limited to, cylinder pressure, fuel mixture, and spark plug gap. Once the voltage to jump the gap is reached, a spark is formed and current flows creating the mass of the spark. Increases in cylinder pressure and spark plug gap, as well as less than ideal mixture ratios (either too rich or too lean) will increase the voltage required to create a spark. In more simple terms, if you step on it, requirement goes up. If you increase your engine's load while towing i.e. more fuel volume enters the cylinder (upping pressure), requirement goes up. If your plugs wear and the gap burns larger, requirement also goes up. As well, any changes that you voluntarily make such as exhaust modifications, bigger carburetors or fuel injectors, camshaft changes, or upping your plug gap to get a bigger spark, all increase the firing voltage requirement.
Some Math
Having more available voltage results in more stored energy in the coil, and since physics dictates energy must be conserved in an equation, we can do some very simple math. Please bear in mind that this is an example to express the basics of the math with simple numbers and leaves out the pages of complex calculations.
Lets compare two hypothetical coils. The math was purposely kept simple for demonstration purposes.
Coil #1 produces a maximum of 50,000 volts with a current of 0.01A (10 milliamps). Total available power would work out to 500 watts (for the spark duration).
The Maximum Number Of Ignition Retries
Coil #2 produces a maximum of 40,000 volts with a current of 0.01A (10 milliamps). Total available power would work out to 400 watts (for the spark duration).
If we have a condition that requires 20,000 volts to initiate a spark, with a spark current of0.0075A (dictated by the circuit resistance - plug wires, distributor, spark plug gap and cylinder pressure):
Coil #1 would work as follows: 500W divided by 20,000 V would equal 0.025A which is 2.5 times the current of the secondary spark since maximum output voltage is not required.
Coil #2 would work as follows: 400W divided by 20,000 V would equal 0.020A which is 2 times the current of the secondary spark since maximum output voltage is not required.
Now for spark duration (we are almost done), our conditions that required 20,000 volts to initialize a spark also dictate that the spark current would be 0.0075A for the particular situation. So Coil #1 would provide 0.025A divided by 0.0075A = 3.33 times the spark duration. Coil #2would provide 0.020A divided by 0.0075A = 2.67 times the spark duration.
Both coils satisfy the requirements of the test, however Coil #1 produces more spark duration. Since a mixture burns in a cylinder, a longer duration spark does two things. It ensures ignition of the fuel mixture and, as the mixture swirls in the cylinder, the spark can be igniting a larger portion of the mixture helping ensure more complete combustion. With high energy ignitions, it is not uncommon to be able to increase your spark plug gap a little to get a larger spark for even better combustion. Aside from ensuring combustion, a good ignition system can improve efficiency by releasing the most energy from the fuel charge and leaving very little to go out in the exhaust.
Maximum Amount Of Ignition Attempts System Is Locked On My Rheem Water Heater
Of course just picking a coil or ignition system that advertises high voltage is half the battle. If the system has less output current than your present system it may not perform any better. A good parameter to look for is maximum available output power/spark.
Maximum Amount Of Ignition Attempts Rheem
Misconceptions
A number of misconceptions have been made over the years. Let's take a minute to review a few popular ones. ' Too hot a spark will burn holes in your pistons ' - not true. Pinging or detonation caused by poor fuel grade, incorrect fuel mixture, or incorrect ignition timing cause this kind of damage. ' Too hot a spark will cause your engine to run too lean and run hot ' - not true either. Fuel mixture alone dictates rich or lean. Too rich and combustion temperature goes down, too lean and it goes up. Too weak a spark can cause a mixture not to burn well leaving behind too much unburned fuel. However, having close to complete combustion of a proper mixture is not harmful. ' Any spark will do to run an engine ' - partly true. If the spark can initiate combustion, the engine will run. Beyond that it is a matter of efficiency. The fact is that there is a finite amount of time for a mixture to burn before the exhaust valves open. As well, the higher the RPM the shorter this time becomes. Here is an analogy to demonstrate this. If you were to take a sheet of paper and light it with a match, the paper will burn in ' x ' amount of time. If you were to use a larger flame to ignite the same sheet of paper, the subsequent larger flame front would consume the paper in a shorter period of time. Both methods will burn the paper no question. But like an engine, if you only have a finite amount of time to complete a burn, you would choose the larger flame. This is not to imply that fuel burns slowly in an engine. Fuel actually burns very quickly, however we are talking about only milliseconds of available time to completely burn in a cylinder between valve openings.

On the other hand, in an ignition timing control operation of an ignition mechanism of a distributor type instead of the ignition mechanism of an electronic spark advance type, the ignition timing is held constant whether the recirculation of exhaust gas is effected or not.
One such ignition timing control apparatus is disclosed, for example, in Japanese Patent Early Laid-open Publication No. Sho 57-179370 and Japanese Utility Model Early Laid-open Publication No. Sho 61-66667. One, which is described in Japanese Patent Early Laid-open Publication No. Sho 57-179370, is designed such that if, at the time a non-operating state of the EGR valve is detected, the engine speed and the value of a signal representing the amount of air intaken are within the ranges of the amount of intaken air and the engine speed on level ground, then the ignition timing is optimally corrected in order to prevent the occurrence of knocking of the engine also on a high land.
Another apparatus, which is described in Japanese Utility Model Early Laid-open Publication No. Sho 61-66667, is designed such that the ignition timing is corrected in accordance with EGR based on the change in the rate of EGR.
There is conventionally an inconvenience in that, since the control means does not have a single kind of ignition timing map, the ignition timing at the time that recirculation of exhaust gas is not effected is excessively spark advanced, thus exerting adverse affects on drivability, emission, etc.
Also, because of the above-mentioned reason, the exhaust gas recirculation mechanism cannot be turned on/off positively depending on driving conditions of the engine and, therefore, improvement was demanded.
Further, even in case the control means is provided with two kinds of ignition timing maps for performing an on/off operation for the exhaust gas recirculation mechanism, there is an inconvenience in that an attempt is made to control the rate of EGR, and the ignition timing is excessively spark advanced or excessively spark halted because the required ignition timing is uselessly changed due to difference in the rate of EGR.
Therefore, an object of the present invention is to provide an ignition timing control apparatus for an engine, in which a duty-controlled EGR rate regulating solenoid valve is disposed midway along an EGR passage intercommunicating an exhaust passage and an intake passage, and by adjusting the ignition timing in accordance with a duty rate which controls the EGR rate regulating solenoid valve, the EGR rate is changed in a non-stage manner and the ignition timing is optimally adjusted in accordance with this EGR rate, thereby enhancing the drivability and obtaining the most appropriate exhaust emission.
In an attempt to achieve the above object, in an engine including an exhaust gas recirculation mechanism for recirculating a part of the exhaust air into the gas intake system, the present invention is characterized in
a duty-controlled EGR rate regulating solenoid valve is disposed midway along an EGR passage intercommunicating the exhaust passage and the intake passage, and means for controlling the activation of the engine ignition mechanism is provided in order to adjust the ignition timing in accordance with a duty rate which is applied to said EGR rate regulating solenoid valve.
According to the constitution of the present invention, since the control means actuates the ignition mechanism in accordance with the duty rate applied to the EGR rate regulating solenoid valve to adjust the ignition timing, the ignition timing can be optimally set when the EGR rate is changed in a non-stage manner and by this, the EGR rate can be positively controlled to enhance the drivability and to obtain the most appropriate exhaust emission.
BRIEF DESCRIPTION OF THE DRAWINGS
One embodiment of the present invention will be described in detail with reference to the drawings, in which:
FIG. 1 is a block diagram of an ignition timing control system apparatus for an engine;
FIG. 2 is a flowchart for explaining the operation of the FIG. 1 system;
FIG. 3 is an explanatory view of an ignition timing map where the EGR duty rate is between 0% and 100%;
FIG. 4 is an explanatory view of an ignition timing map where the EGR duty rate is 0%;
FIG. 5 is an explanatory view of an ignition timing map where the EGR duty rate is 100%; and
FIG. 6 is a block diagram of a conventional ignition timing control system apparatus.
DETAILED DESCRIPTION
FIGS. 1 through 5 show one embodiment of the present invention. In FIG. 1, the numeral 2 denotes an engine, 4 an intake pipe, 6 an intake passage, 8 an exhaust pipe, and 10 an exhaust passage. The intake pipe 4 and the exhaust pipe 8 are interconnected by an EGR pipe 14 forming an exhaust gas recirculation mechanism 12.
This EGR pipe 14 forms an EGR passage 16 for intercommunicating the intake passage 6 and the exhaust passage 10. That is, an EGR inlet port 18 as the start of the EGR passage 16 opens into the exhaust passage 10 and an EGR circulation portion 20 as a terminal of the EGR passage 16 opens into the intake passage 6. Midway along this EGR passage 16, a duty-controlled EGR rate regulating solenoid valve 22 is disposed in order to regulate the rate of EGR by opening and closing the EGR passage 16. This EGR rate regulating solenoid valve 22 is duty-controlled by a control means (ECU) 24. That is, the valve 22 is activated by ECU 24 between a state of 0% of EGR duty (totally closed state) and a state of 100% of EGR duty (totally opened state). By this, the EGR rate effected by the EGR passage 16 can be controlled in a non-stage manner as defined by the continuum of duty rates between 0% and 100%.
Input into this control means 24 are data representing cooling water temperature, intake pipe absolute pressure PM, intake air temperature, throttle opening degree, the number of engine revolution (i.e. engine rotational speed) NE, and a crank angle of the engine from a crank angle sensor 26 attached to the engine 2.
Further, this control means 24 is operated to control the activation of an ignition mechanism 28 of the engine 2 in order to adjust the ignition timing in accordance with the duty rate applied to the EGR rate regulating solenoid valve 22. The control means 24 has an ignition timing map (see FIG. 4) for use at the time the EGR duty is 0% (EGR is in the totally closed state) and an ignition timing map (see FIG. 5) for use at the time the EGR duty is 100% (EGR is in the totally open state). Those ignition timing maps shown in FIGS. 4 and 5 are decided by, for example, the engine rotational speed NE and the intake pipe absolute pressure PM. Accordingly, when the EGR duty is 100%, the FIG. 5 map indicates that the ignition timing is to be spark advanced. For example, the ignition timing is 20 BTDC when the EGR duty is 0% and the ignition timing is 40 BTDC when the EGR duty is 100%, at a certain lattice point defined by the values of NE and PM (see FIGS. 4 and 5) That is, for given values of NE and PM, FIGS. 4 and 5 yield 20° BTDC and 40 ° BTDC, respectively, as functions of NE and PM. Thus, for example, 20° BTDC=f(NE, PM).
And in case a vehicle runs at this lattice point, the ignition timing control at the time the EGR duty is changed between 0% and 100% is decided with reference to the ignition timing map of FIG. 3. That is, for given values of NE and PM, when the EGR duty is something other than 0% and 100%, interpolation is effected with reference to FIG. 3. Accordingly, in case the EGR rate is changed in a non-stage manner, the best ignition timing can be obtained based on the ignition timing decided by the ignition timing maps of FIGS. 3, 4 and 5.
It will be evident from the foregoing and following discussions that ECU 24 can be implemented using a conventional microprocessor circuit.
Next, operation of this embodiment will be described with reference to the flowchart of FIG. 2.
In the control means 24, when a program is started (step 102), first, the data representing the engine rotational speed NE, intake pipe absolute pressure PM, throttle opening degree, cooling water temperature, etc. are input (step 104), and then a duty rate for the EGR rate regulating solenoid valve 22 is calculated from this data (step 106).
Next, the control means 24 is operated to control the activation of the EGR rate regulating solenoid valve 22 in accordance with the calculated duty rate (step 108).
Further, the control means 24 is operated at 110 to control the activation of the ignition mechanism 28 and thereby implement the ignition timing decided based on the ignition timing maps of FIGS. 3 through 5 with reference to the EGR duty rate calculated at 106. That is, the control means 24 is operated to actuate the ignition mechanism 28 at the ignition timing decided by the ignition timing map shown in FIG. 4 when the EGR duty is 0%, the control means 24 is operated to actuate the ignition mechanism 28 at the ignition timing decided based on the ignition timing map shown in FIG. 5 when the EGR duty is 100%, and the control means 24 is operated to actuate the ignition timing mechanism 28 at the ignition timing decided based on the ignition timing map of FIG. 3 when the EGR duty is something other than 0% and 100% (step 110).
As a result, since the EGR rate regulating solenoid valve 22 is duty-controlled by the control means 24, the EGR rate can be changed in a non-stage manner and since the ignition timing is optimally adjusted in accordance with the duty rate applied to the EGR rate regulating solenoid valve 22, the drivability can be enhanced and there can be obtained the most appropriate exhaust emission. Further, since the ignition timing is changed in accordance with the EGR rate, the drivability can be enhanced by positively changing the EGR rate (or turning off the EGR).
Furthermore, since the ignition timing maps of FIGS. 4 and 5 are only, for example, two-dimensional maps of engine rotational speed (NE) X intake pipe absolute pressure (PM), and do not require a three-dimensional map of engine speed NE X intake pipe absolute pressure PM X EGR duty rate, the control means 24 can be simplified and the capacity of the control means 24 can be reduced.
As apparent from the foregoing detailed description, according to the present invention, since a duty-controlled EGR rate regulating solenoid valve is disposed midway along an EGR passage intercommunicating an exhaust passage and an intake passage, and means for controlling the activation of the engine ignition mechanism is provided in order to adjust the ignition timing in accordance with a duty rate applied to the EGR rate regulating solenoid valve, the EGR rate can be changed in a non-stage manner and the ignition timing can be optimally adjusted in accordance with the duty rate applied to the EGR rate regulating solenoid valve, thus enhancing drivability by positively controlling the EGR rate and obtaining the most appropriate exhaust emission.
Although a particular preferred embodiment of the invention has been disclosed in detail for illustrative purposes, it will be recognized that variations or modifications of the disclosed apparatus, including the rearrangement of parts, lie within the scope of the present invention.
Ignition Systems
Basics to High Performance
The job of an ignition system is to generate the spark energy needed to ignite the air/fuel mixture in an engine's cylinder. The main components of this system consist of an ignition coil, coil driver, distributor, spark plug wires, and spark plugs. This page will concentrate on the generation of the high voltage needed to produce a spark, and will begin with a basic ignition style and progress to performance types.
Magnetos
The most basic form of an ignition system is the magneto. Although it was one of the first styles built, it remains in use today. Using the example of a small engine such as a lawn mower or chainsaw, a basic magneto begins with a hub containing magnets which is attached to the crankshaft. As the crankshaft turns these magnets spin past a primary coil of wire to produce a current similar to a generator. The faster the engine runs the more power is generated by the magneto. A set of contacts (points), with a condenser to reduce contact arc wear, switches the current on and off in this primary coil. This process induces a pulse of a few hundred volts into a secondary coil each time the contacts open. The secondary coil has a much higher number of wire turns (typical ratio of 100:1) which acts to multiply the voltage into tens of thousands of volts to produce a spark. The points are activated by a lobe on the crankshaft to produce the spark at the right time (ignition timing). Newer type magnetos use electronic controls instead of points and can offer better timing control. Since magnetos generate their own electricity they are suitable for products that do not have room to carry and recharge batteries, such as lawn mowers, chainsaws, outboard motors and some small displacement motorcycles, etc. Some aircraft still use magnetos (although more complex) as do some racecars. It should be noted that magnetos are not free energy devices. They do place load on a engine like a generator would, with some very large ones actually drawing a moderate number of horsepower.
Kettering Ignition
This battery powered ignition system was first developed by Charles Kettering. A battery replaced the generator portion of a magneto with a battery. A set of contacts (points) and a condenser, switched current from the battery into an ignition coil primary winding. When the points were opened the current would stop and the magnetic field that built up in the primary would collapse, inducing a few hundred volts into the secondary winding of the ignition coil. Again as with a magneto, a turns ratio of 100:1 would yield a secondary voltage that would be in the ten's of thousands of volts. One main advantage of this type of ignition over a magneto is that it can produce strong sparks at low rpm as it doesn't rely on a generator as a primary power source. A condenser is still used to limit the arc current across the points reducing wear. The condenser also helps discharge the coil faster allowing the magnetic field to more fully transfer into the secondary. As engines were built with more cylinders, a device called a distributor was added to the ignition system. A distributor does as the name implies, it distributes the spark to the correct cylinder. A distributor is basically a housing with a shaft that is driven by the engine. Lobes on the shaft activate the points, and a rotor on top of the shaft directs the spark to contacts located in a distributor cap placed on top. From this cap, spark plug wires connect to each individual spark plug.
As expressed earlier, the output of an ignition coil is the result of the primary induced voltage multiplied by the turns ratio. The higher the primary induced voltage (which should not be confused with the battery supply voltage), the higher the coil's output voltage for a given turns ratio will be. The primary induced voltage is a function of the strength of the magnetic field produced by battery current, and charge time (dwell) controlled by the closed time of the points. If a condenser was not present, the primary current would mostly bleed off through the arc produced when the points open, resulting in a very weak spark being produced from the secondary. We will expand on this later as it pertains to performance ignition systems. Aside from the high voltage produced from a coil, the output current is also important as it directly relates to spark duration which does the actual work igniting a fuel mixture.
Electronic Ignition
The initial design of the electronic ignition employed a high voltage transistor to switch current into the ignition coil instead of points. In early designs, a set of points were used to trigger the transistor and since the current required was very low, there would be no contact wear through arcing which allowed longer life of the points. The condenser could be eliminated as the points had no further arcing issues. Utilizing a transistor enables faster switching of the coil primary. This allows higher current transfer to take place resulting in more coil output. Further improvements included the use of a magnetic reluctor pickup to replace mechanical points. This type of pickup uses a small toothed collar to replace the lobes on the distributor shaft. As the teeth pass a bobbin of wire and magnet combination, a small signal is produced to trigger the transistor circuit. Another variation uses Hall Effect technology where the bobbin of wire is replaced by a special transistor. Some distributors were also designed with an optical pickup in which an infrared light beam was interrupted by a notched wheel on the distributor shaft. Some modern ignitions use separate coils for each spark plug which are triggered from sensors directly on the crankshaft and camshaft through an onboard computer.
Inductive Discharge vs Capacitive Discharge Ignition (CD)
All of the above descriptions are examples of Inductive Discharge type ignition systems. The first high performance ignition system design was the Capacitive Discharge Ignition which uses high voltage stored in a capacitor to induce the few hundred volt pulse into the secondary instead of generating it in the primary as with an inductive system. In a CD system a high voltage oscillator circuit charges a capacitor. When it is time for a spark, another circuit discharges the capacitor into the coil primary. The voltage produced from the secondary is in the same proportion as with an inductive system. For example if the capacitor is charged to 400 volts, a 100:1 coil will produce 40,000 volts (or there abouts). CD ignitions have certain limitations depending on design. As an example if the oscillator is not powerful enough, the capacitor will not recharge quick enough and the ignition will have an RPM limitation. As you engineer more powerful oscillators, power consumption also increases. As the size of the capacitor is increased, the output of the ignition also increases, however the oscillator must be made more powerful. Certain tradeoffs must be made in design for a particular application.
Compared to inductive systems of the day, CD systems were more powerful since higher primary voltages could be discharged into the coils. One inherent limitation to a CD system is that the spark duration is short due to small capacitors used. As mentioned earlier, spark duration does the actual work burning an air fuel mixture, the voltage is used to initialize current flow across a spark plug gap. Due to the high primary currents of an inductive system, spark duration is naturally longer. Some Manufacturers of CD ignition systems provide multiple sparks to increase overall spark duration. Of course, as mentioned before, capacitors take time to charge up so there are limitations as to what RPM levels a CD system can maintain multiple sparks.
Today with improvements in technology, inductive ignition systems can be made more powerful with special transistors (Mosfets) switching the coil. These devices have higher breakdown/clamping voltages which allow the primary voltage to increase ( 550+ volts) resulting in higher secondary voltages. This coupled with the inherent long duration makes for a powerful ignition which has the capability of also going multi spark. Inductive ignition systems are emerging as the new high power ignition systems.
More Voltage ?
There is some argument that output voltage of an ignition system does not have to exceed 35,000 to 40,000 volts as normal demand doesn't exceed this. The voltage required to initiate a spark across a spark plug gap depends on a number of conditions including, but not limited to, cylinder pressure, fuel mixture, and spark plug gap. Once the voltage to jump the gap is reached, a spark is formed and current flows creating the mass of the spark. Increases in cylinder pressure and spark plug gap, as well as less than ideal mixture ratios (either too rich or too lean) will increase the voltage required to create a spark. In more simple terms, if you step on it, requirement goes up. If you increase your engine's load while towing i.e. more fuel volume enters the cylinder (upping pressure), requirement goes up. If your plugs wear and the gap burns larger, requirement also goes up. As well, any changes that you voluntarily make such as exhaust modifications, bigger carburetors or fuel injectors, camshaft changes, or upping your plug gap to get a bigger spark, all increase the firing voltage requirement.
Some Math
Having more available voltage results in more stored energy in the coil, and since physics dictates energy must be conserved in an equation, we can do some very simple math. Please bear in mind that this is an example to express the basics of the math with simple numbers and leaves out the pages of complex calculations.
Lets compare two hypothetical coils. The math was purposely kept simple for demonstration purposes.
Coil #1 produces a maximum of 50,000 volts with a current of 0.01A (10 milliamps). Total available power would work out to 500 watts (for the spark duration).
The Maximum Number Of Ignition Retries
Coil #2 produces a maximum of 40,000 volts with a current of 0.01A (10 milliamps). Total available power would work out to 400 watts (for the spark duration).
If we have a condition that requires 20,000 volts to initiate a spark, with a spark current of0.0075A (dictated by the circuit resistance - plug wires, distributor, spark plug gap and cylinder pressure):
Coil #1 would work as follows: 500W divided by 20,000 V would equal 0.025A which is 2.5 times the current of the secondary spark since maximum output voltage is not required.
Coil #2 would work as follows: 400W divided by 20,000 V would equal 0.020A which is 2 times the current of the secondary spark since maximum output voltage is not required.
Now for spark duration (we are almost done), our conditions that required 20,000 volts to initialize a spark also dictate that the spark current would be 0.0075A for the particular situation. So Coil #1 would provide 0.025A divided by 0.0075A = 3.33 times the spark duration. Coil #2would provide 0.020A divided by 0.0075A = 2.67 times the spark duration.
Both coils satisfy the requirements of the test, however Coil #1 produces more spark duration. Since a mixture burns in a cylinder, a longer duration spark does two things. It ensures ignition of the fuel mixture and, as the mixture swirls in the cylinder, the spark can be igniting a larger portion of the mixture helping ensure more complete combustion. With high energy ignitions, it is not uncommon to be able to increase your spark plug gap a little to get a larger spark for even better combustion. Aside from ensuring combustion, a good ignition system can improve efficiency by releasing the most energy from the fuel charge and leaving very little to go out in the exhaust.
Maximum Amount Of Ignition Attempts System Is Locked On My Rheem Water Heater
Of course just picking a coil or ignition system that advertises high voltage is half the battle. If the system has less output current than your present system it may not perform any better. A good parameter to look for is maximum available output power/spark.
Maximum Amount Of Ignition Attempts Rheem
Misconceptions
A number of misconceptions have been made over the years. Let's take a minute to review a few popular ones. ' Too hot a spark will burn holes in your pistons ' - not true. Pinging or detonation caused by poor fuel grade, incorrect fuel mixture, or incorrect ignition timing cause this kind of damage. ' Too hot a spark will cause your engine to run too lean and run hot ' - not true either. Fuel mixture alone dictates rich or lean. Too rich and combustion temperature goes down, too lean and it goes up. Too weak a spark can cause a mixture not to burn well leaving behind too much unburned fuel. However, having close to complete combustion of a proper mixture is not harmful. ' Any spark will do to run an engine ' - partly true. If the spark can initiate combustion, the engine will run. Beyond that it is a matter of efficiency. The fact is that there is a finite amount of time for a mixture to burn before the exhaust valves open. As well, the higher the RPM the shorter this time becomes. Here is an analogy to demonstrate this. If you were to take a sheet of paper and light it with a match, the paper will burn in ' x ' amount of time. If you were to use a larger flame to ignite the same sheet of paper, the subsequent larger flame front would consume the paper in a shorter period of time. Both methods will burn the paper no question. But like an engine, if you only have a finite amount of time to complete a burn, you would choose the larger flame. This is not to imply that fuel burns slowly in an engine. Fuel actually burns very quickly, however we are talking about only milliseconds of available time to completely burn in a cylinder between valve openings.
High Energy Ignition For Any Car ?
Applications that benefit most from high energy ignition systems are vehicles where engines are placed under loads such as trailer towing, motor home applications, and fully loaded vehicles such as work trucks. Sports and performance cars that have undergone modifications are also candidates for ignition improvements and should consider such to get the most from other engine modifications. With the emerging use of alternate fuels come increased need for good ignition due to the narrower window of flammability of the fuels. For the rest, the best advice is to keep your current vehicle's ignition system in good repair. Aside from a regular tune up, consider a high quality performance spark plug wire set. This simple purchase can ensure that your stock ignition's potential is able to reach your spark plugs unimpeded.
At Aurora, we are constantly developing new technology for ignition system design. We have always worked with Inductive Discharge platforms due to inherent long spark duration. With custom designed coils, a match between coil and driver electronics has yielded what we feel are optimal results. Our current designs incorporate microprocessors running our progressive dwell software enabling wide performance curves. In addition to our ignition coil and controller system development, high performance spark plug wire design has been in the forefront of our research. Well designed ignition wires are necessary to deliver energy efficiently from whatever ignition system may be in use.
Maximum Amount Of Ignition Attempts
This article was intended to give a basic understanding of ignition systems, primarily the generation of spark. Deliberate attempts were made to keep technical content to a minimum for easier understanding.
© 2005 Aurora electronics Ltd. All rights reserved. All material contained in this website is protected under copyright law and may not be copied in whole or in part by without express written permission of Aurora Electronics Ltd.
Aurora,High Performance Ignition Systems, Aurora,ignition,coils,performance coils,ignition coils